Patients with progressive muscle weakness (muscular dystrophy) often suffer from major limitations in their mobility. The "Autonomyo" exoskeleton can support the weakened muscles. The additional power comes from small motors with specially integrated magnetic torque sensors.
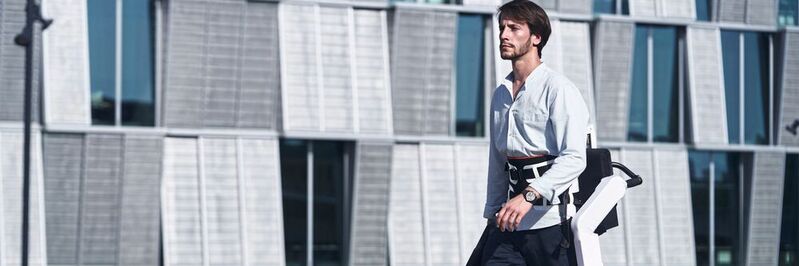
"When muscle weakness manifests in the legs, walking becomes harder and harder, and eventually it doesn't work at all without supports," explains Mohamed Bouri, head of the Rehabilitation and Assistive Robotics (Reha Assist) research group at the Lausanne University of Technology in Switzerland (EPFL).
"The muscles still function, but they no longer have enough strength for a stable stance or independent leg movement. This has an enormous impact on range of motion and quality of life. A hemiplegia after a stroke has similar effects. Our goal was to overcome these limitations as much as possible with the help of a motorized assist device that allows patients to contribute to their own movements."
How does the new development work?
Common exoskeletons, which enable paraplegics to walk without crutches, often weigh over 40 kg. The "Autonomyo" developed by Reha Assist is significantly lighter at only 25 kg and works by incorporating the patient's weakened but still partially functioning musculoskeletal system. It is attached to the torso with a corset and to the legs with cuffs. On each side, three small motors provide the power that the muscles lack for movement. One motor each is responsible for flexion and extension of the hip and knee. The third small motor supports abduction and adduction of the leg in the hip joint, i.e. lateral movement away from the body's central axis. The motors thus help the patient maintain balance and walk upright. A recent clinical study with, among others, people with walking disabilities showed that the exoskeleton worked as intended: it provided freedom of movement according to the user's intentions and did not negatively affect joint range of motion or gait cadence.
The exoskeleton can support weakened muscles and allows an intuitive movement sequence that follows the natural one.
"The first trigger to go is expressed in a small change in the position of the lower limbs," says Mohamed Bouri. This is detected by combining information from an inertial measurement unit, eight load sensors on the soles of the feet, and the encoders on the motors that serve as joint position sensors, he said. This data, moreover, helps support balance. According to Mohamed Bouri, when walking, the interaction between the exoskeleton and its user is crucial. A magnetic torque sensor developed by Faulhaber (see company box) detects this interaction, which is important for the support strategy.
Magnetic torque sensor as an alternative to strain gauges
Strain gauges that are deformable by the applied force are usually used for torque measurement. A design weakness is the adhesive connection for their application. Developers at Faulhaber therefore replaced them with a high-resolution magnetic measuring system, with which a deviation of less than 1.5 % can be achieved in the measuring range of +/- 30 Nm. The magnetic torque sensor thus provides a highly precise value of the reaction torque in the walking movement, which is of central importance for controlling the exoskeleton. "Adapting the device to individual patients requires a highly differentiated calibration of the overall system. Based on the different parameters and the feedback from the movement, the software calculates the control signals for the drives. The type and extent of support provided by the small motors is then determined on the basis of this information," explains the head of the Reha Assist research group.
What are the requirements for the drive power?
At the heart of the six drive units installed is the compact 3274 BP4 brushless motor with a diameter of 32 mm, which delivers a rated torque of 158 mNm. Its power is transmitted by a 42 GPT planetary gearhead with a shaft specially manufactured for this application. The IE3 encoder supplies the position data to the controller. The magnetic torque sensor is integrated in the gears of the four small motors for the flexion and extension movements of the knee and hip.
THE DRIVE SPECIALISTS FROM SCHÖNAICH
Faulhaber specializes in the development, production and use of high-precision miniature and microdrive systems, servo components and controllers with an output power of up to around 250 watts. This includes the realization of customer-specific complete solutions as well as an extensive range of standard products such as brushless motors, DC micromotors, encoders and motion controllers. According to the company, the Faulhaber brand stands for high quality and reliability in complex and demanding application areas such as medical technology, factory automation, precision optics, telecommunications, aerospace and robotics. From the powerful DC motor with 224 mNm continuous torque to the filigree micro drive with an outer diameter of 1.9 millimeters, the Faulhaber standard portfolio includes more than 25 million options for putting together an optimal drive system for an application. This modular technology is also the basis for modifications in order to be able to respond to special customer requests for special designs.
Search for suitable supplier not difficult
The requirements for the drive units are typical for Faulhaber small motors: high performance with the smallest possible volume and weight, precision, reliability and long service life. According to Mohamed Bouri, the search for the right supplier was not particularly difficult: "By defining the specifications, the selection of motors under consideration was already very manageable. The cross-faculty astrophysics research group at our university already works with Faulhaber, so they made convincing recommendations. In addition, Faulhaber was able to develop the torque sensor in a very short time, which was very important for our project."
What development potential does the novelty have?
For the time being, the magnetic torque sensor is not part of the series products and has so far only been manufactured in small quantities for the application described with the exoskeleton. However, other areas of application are conceivable where very precise torque values need to be measured, for example in haptic applications such as robot assistance in the operating room, where the surgeon guides the instrument and the machine provides force and precision. The sensor lends itself to documentation in quality assurance.
Source: Walking without crutches with small motors and torque sensor (vogel.de) (09.12.2022)